
- Home
- Top Stories
- Why Indian Pharma Isn't Able To Break...
Why Indian Pharma Isn't Able To Break Free From Dependence On Chinese Bulk Drugs
Despite the government's efforts, the Indian pharmaceutical industry remains uncertain about the competitiveness of locally manufactured bulk drugs against China's.
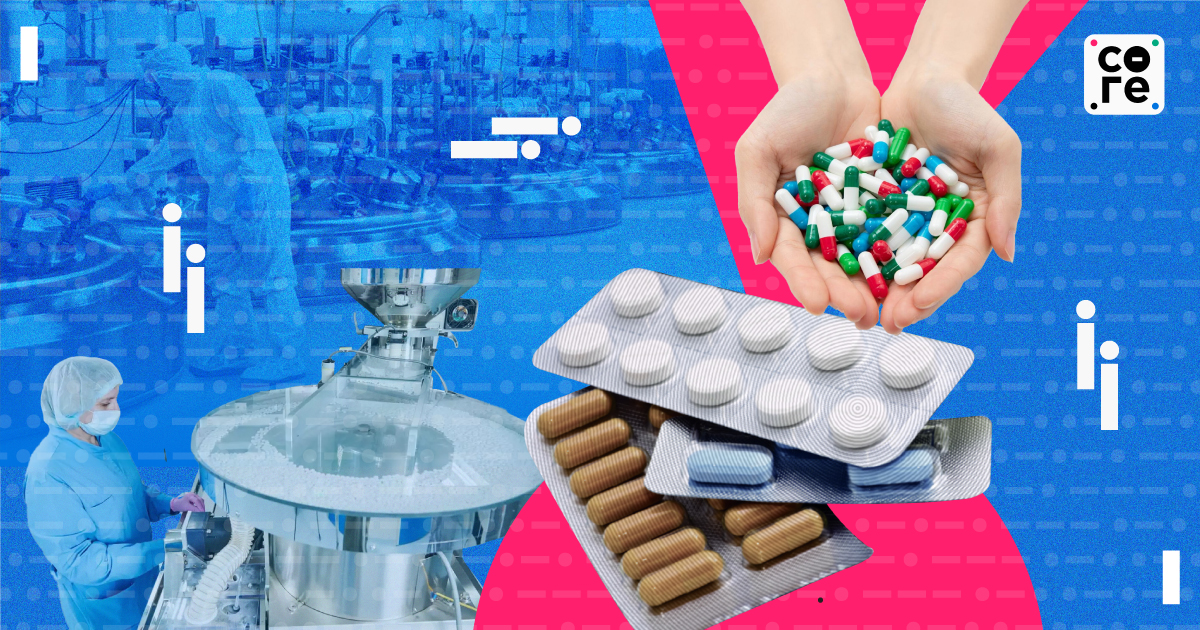
It was March of 2020, only a few days before the World Health Organization declared Covid-19 a pandemic. India spooked the world by deciding to ban the export of paracetamol and a cluster of other commonplace drugs. Pharmacists in the UK, for one, were advised against dispensing more than a single packet of paracetamol per customer. Soon the US, too, grew antsy, and its secretaries started dialling up their peers in India. The Indian government, on the other hand, had not offered an explicit reason for its decision, yet it was clear as day that it was afraid of running short of essential drugs in the face of a pandemic lurking to metastasise.
The world?s pharmacy, so to speak, lay exposed. India?s pharma giants may have mastered the art of making generic medicines and selling them cheaply around the world, but to make those very drugs, they depended heavily on raw materials ? known as bulk drugs or active pharmaceutical ingredients (APIs) ? imported from China.
The dependence was critical: India imported 70% of its API requirements from China at that time. A paper estimated that there were at least 70 APIs for which India was dependent on China for 100% of imports. So when the lockdown in China?s Hubei pr...
It was March of 2020, only a few days before the World Health Organization declared Covid-19 a pandemic. India spooked the world by deciding to ban the export of paracetamol and a cluster of other commonplace drugs. Pharmacists in the UK, for one, were advised against dispensing more than a single packet of paracetamol per customer. Soon the US, too, grew antsy, and its secretaries started dialling up their peers in India. The Indian government, on the other hand, had not offered an explicit reason for its decision, yet it was clear as day that it was afraid of running short of essential drugs in the face of a pandemic lurking to metastasise.
The world’s pharmacy, so to speak, lay exposed. India’s pharma giants may have mastered the art of making generic medicines and selling them cheaply around the world, but to make those very drugs, they depended heavily on raw materials — known as bulk drugs or active pharmaceutical ingredients (APIs) — imported from China.
The dependence was critical: India imported 70% of its API requirements from China at that time. A paper estimated that there were at least 70 APIs for which India was dependent on China for 100% of imports. So when the lockdown in China’s Hubei province, which was at the epicentre of the global outbreak, forced factories to shut, Indian drugmakers were left scrambling to source raw materials, so much so that India had to briefly impose an export ban.
The overdependence on China for APIs has always been a problem, but only in the aftermath of the pandemic-induced supply chain shocks did the government and industry decide to do something about it. In July 2020, the Indian government announced a production-linked initiative (PLI) to promote domestic manufacturing of bulk drugs. Four years on, a myriad of problems — from red tape to environmental concerns — put paid to those hopes and Indian drugmakers continue to rely on APIs from China.
Trials And Tribulations
Despite the industry’s efforts and the government's push to boost domestic manufacturing, India's imports of APIs from its neighbour have only gone up. Last December, the Minister of State for Chemicals and Fertilisers confessed as much in the parliament. He noted that imports from China grew from Rs 23,273 crore in 2021-22 to Rs 25,551 crore in 2022-23, an increase of 9.78%. Reji K Joseph, an associate professor at the Institute for Studies in Industrial Development (ISID), who has been tracking the fall and rise of India's API industry, estimates that China's share in India's import of APIs has also grown from 70% in pre-pandemic times to 72% post-pandemic.
So where did India fall short? It has only been a year of production under the PLI scheme. "So this is a bit early to arrive at some firm conclusions, but we can give some indications on how the scheme is going as of now," Joseph told The Core.
Industry apathy is one reason. A working paper that Joseph co-authored with Ramaa Arun Kumar noted that the response of the industry to this scheme was not encouraging. Though the PLI offered incentives worth Rs 69,400 million over the period of six years to ramp up manufacturing of select APIs, the scheme design was short-sighted.
For Indian pharma to take up API manufacturing, it must do so in a way that allows it to compete with China’s cut-rate prices. According to Viranchi Shah, president of the Indian Drug Manufacturers' Association (IDMA), China is a formidable competitor. Considering China's scale of manufacturing, state subsidies, and technological prowess, it is understandable why our neighbour can mass-produce bulk drugs at prices 20-30% lower than international rates.
India must invest in technology to be competitive. In the absence of such support in the PLI scheme, pharma companies face a dilemma. “Smaller firms, which specialise in API manufacturing in India, do not have that kind of money to invest in R&D. Developing technology is not an overnight business. You will have to invest consistently for many months and years and sometimes you may have to fail,” Joseph said.
Even if a company decides to upgrade its technology, drug manufacturers face further challenges in the form of red tape. The API industry has been labelled one of the most polluting in India by the Pollution Control Board. As a result, every time a company decides to change its product mix or add machinery, it must seek fresh approvals. Shah said that delayed clearances are one of the biggest challenges for domestic API manufacturing. “We have requested the government time and again that we are not saying that norms need to be diluted or that pollution has to be accepted, but at least the speed at which those clearances are done has to be improved,” Shah told The Core. At present, fresh approvals take anywhere from four months to a year.
Environmental issues were, in fact, at the centre of the conflict that led to the unravelling of Hyderabad’s Pharma City, a park for bulk drug manufacturers proposed by the Telangana government. It had promised to acquire land so companies do not have to deal with environmental regulations. However, land acquisition got mired in local protests and the government scrapped the project altogether in February this year. A local API manufacturer told The Core that he wasn’t surprised. “Nonetheless, it’s a drawback. There is demand for locally made bulk drugs, but we are unable to expand to ramp up production,” he said on condition of anonymity.
Mahesh H Doshi, former president of Indian Drug Manufacturers’ Association, who is also an API manufacturer, shared similar concerns. He told The Core that the Indian government has to take a long-term view of the situation, and schemes that last for barely six years don’t suffice when competing against a player like China.
Ghosts Of The Past
Shah said that the industry’s outlook towards manufacturing APIs is “cautious”: “They are seeing an opportunity; they are also seeing that there are a lot of challenges.”
The abundant caution might have something to do with the ghosts of the past. Till the early 1990s, India was self-reliant in manufacturing bulk drugs. But by the mid-1990s, as the markets opened up and the government removed import duties, China flooded Indian markets with cheaper APIs. Indian manufacturers could not compete, and the industry, in turn, was decimated.
Jaijit Bhattacharya, president of the Centre for Digital Economy Policy Research, told The Core that the first thing India needs to ensure is that it must not reduce import tariffs. “There should be protection against the predatory pricing of foreign players who are dumping their products into India. There should be trade remedies in place,” Bhattacharya said.
Joseph, on the other hand, feels it is counterintuitive. India’s pharma industry is export-oriented, so any strict regulations on sourcing drugs will cause India to lose its leadership in generic medicines. As per him, the only way forward is pouring money into R&D and developing new technologies fast, so that India can truly compete with China.
Whatever the way forward might be, the status quo suggests that little has changed and there isn’t a long-term plan to solve the API problem. India is still dependent as ever on China for most of its APIs, and the oft-repeated quote of Cipla chairman YK Hamied is as haunting as ever: “If China decided one bright day to stop export to India, we would be finished.”
Read More
Korean Is The Hottest Trend In India’s Noodles Market, But FMCGs Aren’t Banking On It For Growth
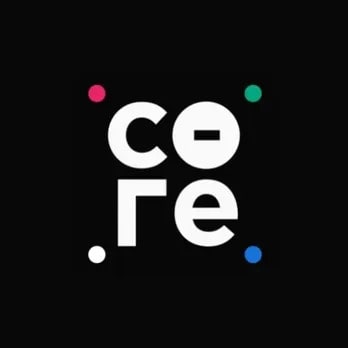
Despite the government's efforts, the Indian pharmaceutical industry remains uncertain about the competitiveness of locally manufactured bulk drugs against China's.