
India’s EV Two-Wheeler Segment Has A Safety Crisis On Its Hands
With over 1 million electric two-wheelers sold in India in 2024, the sector is booming. But beneath this growth lies a pressing concern—safety
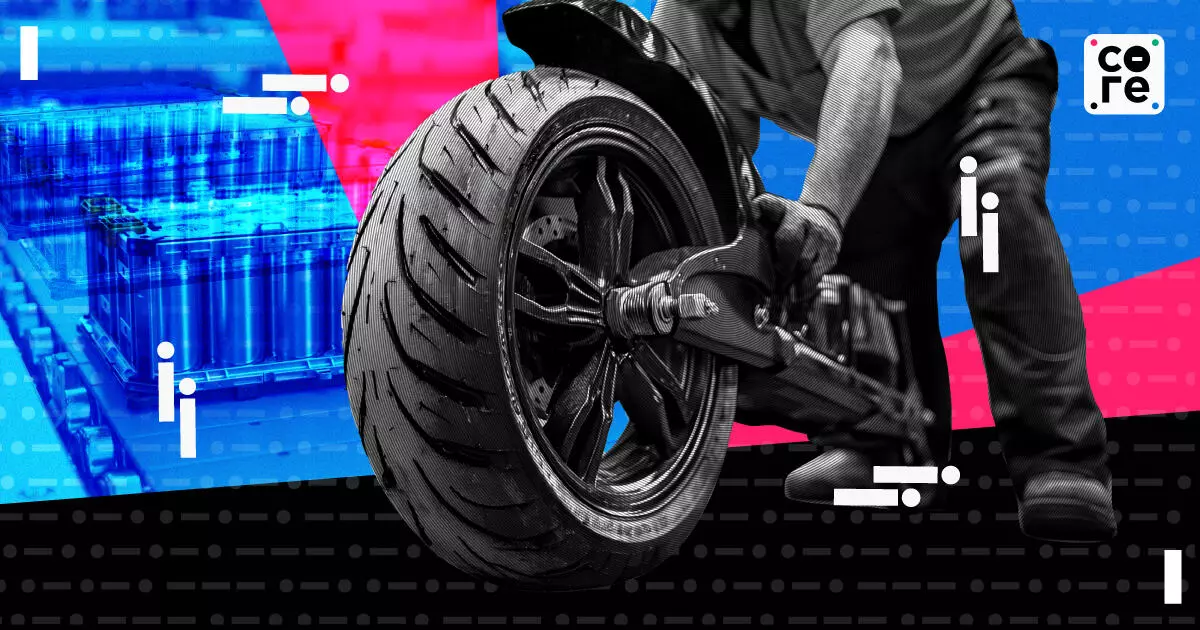
In 2024, India reached a significant milestone, with over 2 million electric vehicles (EVs) entering the roads —most of them two-wheelers. This rapid growth hasn’t been without challenges, especially regarding safety.
To address this, the government updated its safety and testing standards in late 2022 with stricter benchmarks for EV batteries. Known as AIS-156 and AIS-038, these standards were introduced under the Central Motor Vehicle Rules.
Now EV two-wheelers (2Ws) must go through advanced thermal propagation tests to ensure that a single cell failure must not spread to the rest of the pack, and randomised post-production checks to ensure consistent quality. The new standards aim to tackle recurring issues like thermal runaway in EV batteries and bring much-needed accountability to an industry under scrutiny.
What led to these new rules?
A series of troubling incidents in the recent past have exposed vulnerabilities in the industry. The spate of EV fires, including those involving Ola Electric in 2022 and 2023, and a tragic Okinawa scooter fire incident in Vellore in 2022 that claimed two lives, brought safety concerns to the forefront. These fires were a symptom of a larger systemic issue that ail...
In 2024, India reached a significant milestone, with over 2 million electric vehicles (EVs) entering the roads —most of them two-wheelers. This rapid growth hasn’t been without challenges, especially regarding safety.
To address this, the government updated its safety and testing standards in late 2022 with stricter benchmarks for EV batteries. Known as AIS-156 and AIS-038, these standards were introduced under the Central Motor Vehicle Rules.
Now EV two-wheelers (2Ws) must go through advanced thermal propagation tests to ensure that a single cell failure must not spread to the rest of the pack, and randomised post-production checks to ensure consistent quality. The new standards aim to tackle recurring issues like thermal runaway in EV batteries and bring much-needed accountability to an industry under scrutiny.
What led to these new rules?
A series of troubling incidents in the recent past have exposed vulnerabilities in the industry. The spate of EV fires, including those involving Ola Electric in 2022 and 2023, and a tragic Okinawa scooter fire incident in Vellore in 2022 that claimed two lives, brought safety concerns to the forefront. These fires were a symptom of a larger systemic issue that ails India’s EV two-wheeler industry and could derail India’s EV ambitions.
In October 2023, an Ola S1 electric scooter caught fire in Pune, triggering a nationwide debate about the safety of India’s EVs. A video of the flaming scooter quickly went viral, spreading panic among Ola’s customers.
The company claimed that the fire was caused by an “aftermarket part” installed by the owner. While this shifted the blame to user error, it left unanswered questions about whether flaws in the scooter’s internal systems played a role in the incident.
According to the sources The Core spoke to, these incidents exposed gaps in oversight and quality control, forcing regulators to act decisively to restore consumer trust and ensure the safety of India’s growing EV market.
But what’s Ola got to do with all this? As it was the market leader in 2022, the company became a focal point in this wave of scrutiny. But the Ola fire incident in Pune wasn’t just an isolated incident and the problem isn’t only limited to Ola’s scooters.
EV Fires: A Wake-Up Call
The surge in EV fires prompted the Indian government to launch an investigation. It tasked the Defence Research and Development Organisation (DRDO) to investigate the causes of these fires. The DRDO’s findings weren’t fully revealed to the public, but it did lead to the introduction of the AIS-156 and AIS-038 standards.
For the uninitiated, the Automotive Industry Standards (AIS) are regulatory guidelines for the safety, performance, and emissions of vehicles in India. These standards are developed by the Automotive Research Association of India and the International Centre for Automotive Technology, in collaboration with government bodies such as the Ministry of Road Transport and Highways. AIS plays a crucial role in certifying the safety and quality of both 2W and four-wheeler (4W) EVs before they are allowed on Indian roads.
AIS-156, a subset of these standards, focuses exclusively on the safety of EV batteries. It sets benchmarks for thermal management and battery performance and safeguards against thermal runaway, an overheating phenomenon that has been a major contributor to EV fire incidents.
Industry and policy experts, and EV manufacturers TheCore spoke to pointed to three critical factors that amplified safety issues.
First, the rapid push for electrification has often come at the expense of rigorous safety testing. “In the race to capture market share, manufacturers sometimes expedite product development timelines, leading to insufficient quality checks,” said a former Ola Electric employee on the condition of anonymity.
Second, significant deficiencies in Battery Management Systems (BMS) worsen these problems. An expert from WRI India, a policy and research organisation, explained how inadequate BMS designs fail to effectively regulate battery parameters, increasing the risk of thermal runaway.
“The BMS is like the brain of the battery,” said Dr Parveen Kumar, program head - Sustainable Batteries at WRI India. “If it is not robust, even minor voltage or temperature fluctuations can lead to catastrophic failures.”
Third, Nickel Manganese Cobalt (NMC) and Lithium Iron Phosphate (LFP) batteries are currently the two dominant chemistries used in the batteries in India’s EV industry. Each has distinct advantages and drawbacks. NMC batteries are prized for their high energy density, delivering extended range and compact designs — features highly sought after in two-wheelers and passenger vehicles. However, NMC’s Achilles’ heel lies in its susceptibility to thermal instability. In high-temperature environments, like those in India, NMC batteries are more prone to thermal runaway, a dangerous condition where the battery uncontrollably overheats, potentially leading to fires. This vulnerability arises from the cobalt and nickel components, which, while enhancing energy density, reduce thermal stability.
In contrast, LFP batteries are chemically more stable and less likely to experience thermal runaway. Their iron-based composition allows them to withstand higher temperatures and over-use scenarios without significant safety risks. LFP batteries are less energy-dense, which means they give lesser mileage. To match the mileage of NMC batteries, LFP batteries would require larger packs. This would make the vehicle overall more expensive. But their safety and longer lifecycles make them ideal for public transport buses and utility vehicles.
“The chemistry debate is not trivial,” explained Dr Kumar of WRI India. “For high-temperature climates like India, LFP is the safer option by far. Its stability under varying voltage and thermal conditions reduces the likelihood of catastrophic failures.”
China has already moved to LFP batteries for most high-risk EV segments, citing safety as a priority. “India needs to take a cue from China,” said a venture capitalist (VC) based in the Netherlands with investments in EV startups globally. “We’ve seen how NMC’s thermal risks have played out in the Indian context. A transition to LFP would mitigate many of these incidents.”
The VC asked to remain anonymous as he didn’t want to be seen publicly commenting on big competitors.
Despite the safety benefits of LFP, many Indian manufacturers depend heavily on NMC, driven by its superior range and performance metrics. This preference stems from a mindset deeply rooted in India’s automotive culture, where ‘mileage per litre’ in the petrol era has seamlessly transitioned to ‘range per charge’ in the EV world. According to the CTO of a large EV manufacturer who spoke off the record, this demand for longer ranges has pushed OEMs to prioritise NMC batteries, even though they come with significant thermal risks.
“Indian consumers have traditionally been hyper-focused on range,” Dr Kumar explained. “This pressure has undoubtedly influenced manufacturers to overlook safety for higher energy density, which exacerbates the problem.”
This argument might seem like shifting the blame to the user, but it reflects a broader problem within the industry — a mismatch between consumer expectations and the safety requirements in the EV world. Fortunately, as regulatory scrutiny intensifies and government policies evolve, Indian EV makers are beginning to move away from their overreliance on NMC.
The NMC Vs LFP Debate
India's two-wheeler EV market has experienced significant growth, with sales reaching approximately 1 million units in the financial year 2024 (FY24). According to the NITI Aayog's report on Advanced Chemistry Cell Battery Reuse and Recycling, India's battery demand for EVs is projected to reach approximately 381 GWh by 2030, making up 63% of the total cumulative demand for batteries across all segments.
This includes grid storage and consumer electronics, with electric two-wheelers alone expected to require over 33 GWh annually by 2030. While two-wheelers continue to dominate India’s EV market, with over 1.2 million units sold in 2024 alone (accounting for nearly 60% of total EV sales), electric three-wheelers (E3Ws) are also witnessing rapid adoption. In the same year, E3W sales reached 694,466 units, growing 18% year-on-year, driven by their increasing use in passenger and cargo transport. The latter segment, in particular, has seen a 45% rise, propelled by the booming logistics and e-commerce sectors.
Despite their differing use cases—two-wheelers serving urban commuters and three-wheelers addressing last-mile transport—the safety and quality challenges around battery systems remain similar. Both segments heavily rely on cost-sensitive battery options, raising concerns about thermal stability, BMS reliability, and long-term safety as demand scales faster than infrastructure and regulation can keep up. Currently, the battery chemistry split in India heavily leans towards NMC batteries, which account for approximately 74% of the electric 2W market, as explained by Kumar from WRI India. These batteries are primarily used in two-wheeler and passenger EV segments due to their higher energy density, which supports compact designs and extended range. LFP batteries represent about 54% of the overall EV market, dominating the bus and commercial vehicle sectors because of their superior thermal stability and safety. The remaining 9% comprises other chemistries, such as Nickel Cobalt Aluminum and Lithium Titanium Oxide, deployed in niche applications requiring ultra-fast charging.
While 2W EVs largely rely on NMC batteries due to their compact size and energy density, 4W EVs take a different approach to safety and performance. Globally and in India, 4W EVs increasingly use Lithium Iron Phosphate (LFP) batteries for their superior thermal stability, despite their lower energy density. Manufacturers like Tata Motors in India and Tesla for its standard-range models globally favour LFP because they prioritize safety and longevity over compactness and range.
Another key distinction lies in thermal management and BMS. Most 4W and electric 3W EVs are equipped with advanced liquid-cooling systems to maintain optimal battery temperatures, even in extreme conditions. In contrast, 2W EVs often rely on air-cooling or passive thermal management systems, which are less effective in controlling overheating. Although 4W manufacturers can justify higher costs for safety due to their premium pricing, 2Ws cater to a cost-sensitive market, making it challenging to implement advanced safety systems without increasing the vehicle’s price.
In two-wheeler EV scooters, battery capacity typically ranges between 2.5kWh and 4kWh. A kilowatt-hour (kWh) represents the amount of energy a battery can store and deliver over time. For instance, a 3kWh battery pack can theoretically deliver 3 kilowatts of power for one hour. This measure directly impacts the scooter’s range and performance, making kWh a key metric for consumers and manufacturers alike.
"The 3kWh packs we use in our scooters are engineered to balance range and safety, but they rely on sophisticated BMS for effective thermal management," explained the CTO of the two-wheeler EV manufacturer quoted earlier in the story. This capacity ensures a range of 85-110 km per charge under standard conditions, a key selling point for urban commuters. The choice of battery chemistry and BMS implementation plays a critical role in achieving this balance, especially in high-frequency usage scenarios like delivery fleets.
According to Yuma Energy, which powers Yulu's battery-swapping network, delivery fleets have reported no significant fire safety incidents due to their advanced real-time battery monitoring systems. "Our batteries are monitored 24/7 through an AI-powered analytics platform," said Muthu Subramanian, Managing Director at Yuma Energy. "This ensures any anomaly is flagged and addressed before it escalates."
Yuma has also built a large charging infrastructure over the years, with the capacity to support over 1.5 million swaps per month as of 2024, primarily serving Yulu’s delivery fleet and urban mobility solutions. "Battery-swapping reduces risks because controlled charging environments eliminate many of the variables that lead to incidents in user-managed charging setups," Subramanian added.
Battery-swapping offers a convenient alternative to charging stations where users can exchange depleted batteries for fully charged ones within minutes, eliminating the need for prolonged charging times. Unlike charging stations, where users plug in their vehicles and wait for the battery to recharge, swapping stations provide ready-to-use batteries, making them particularly effective for high-usage scenarios like delivery fleets.
However, this model has struggled to gain traction in the consumer EV market due to the lack of standardisation across manufacturers. "Standardising battery packs for swapping might streamline infrastructure, but it limits innovation in form factors and designs," explained the venture capitalist familiar with EV policy quoted earlier.
Subramanian of Yuma further added that while swapping infrastructure works well for fleet applications, consumer adoption would require significant alignment between OEMs, regulators, and infrastructure providers. "Without a unified approach, it’s hard to scale swapping for personal EVs," he said. India has largely missed the opportunity to establish a robust battery-swapping ecosystem for personal EVs, primarily due to systemic challenges and infrastructure limitations. Because of a significant charging infrastructure gap, consumers rely heavily on home-installed charging setups due to space constraints in public spaces in urban areas, which makes installing both charging and swapping stations challenging.
Despite these setbacks, the focus has now shifted toward developing localised battery manufacturing capacities.
Building Local Battery Ecosystems
Several two-wheeler EV manufacturers in India are now transitioning from importing fully assembled battery packs to local assembly and production, aiming to reduce costs and improve supply chain resilience.
Ola Electric, for instance, has invested heavily in its NMC battery packs, with Bhavish Aggarwal, the company’s CEO, promising to localise battery manufacturing at scale. The company’s battery packs boast a capacity of 3.92 kWh, offering a range of up to 181 km on a single charge.
"Local assembly is not just about cost savings; it’s about gaining control over quality, ensuring compliance with safety standards, and driving innovation specific to the Indian market," explained a former Ola employee. "When we assemble locally, we not only reduce our reliance on imports but also build the capacity to adapt and refine battery technology based on real-world performance and regulatory requirements."
This shift is critical for the Indian EV industry as it seeks to reduce reliance on Chinese imports, which currently dominate the battery supply chain. "India’s dependency on imported battery packs has been a bottleneck for scaling production sustainably," added Kumar of WRI India.
However, expanding battery capacity and assembling cells domestically alone won’t solve the problem of EV fires and safety incidents. While LFP chemistries are inherently safer than NMC, safety in the Indian EV context also depends heavily on advancements in BMS.
According to the CTO of the leading two-wheeler EV manufacturer mentioned earlier, many OEMs compromise on BMS by only integrating sensors at the battery pack level, not the cell level, to reduce costs. "This kind of cost-cutting, though it brings cheaper EVs to the market, compromises long-term safety," he warned.
A robust BMS acts as the brain of the battery, monitoring parameters such as temperature, voltage, and current in real-time to prevent thermal runaways and other failures. Despite its critical importance, many Indian manufacturers allocate only 3-5% of the vehicle’s total cost to BMS, which translates to a relatively small share of the final price, according to the CTO of an EV firm quoted earlier. Kumar of WRI said that investing in advanced BMS with real-time monitoring capabilities and AI-powered analytics could dramatically reduce incidents.
Testing And Approval Gaps
Another pressing issue in the two-wheeler EV segment is the significant gaps in the testing and approval process for scooters and battery cells. According to a 2022 report by CNBC-TV18, several top electric two-wheeler manufacturers in India have allegedly exploited loosely framed rules, potentially contributing to the rise in safety incidents.
The CNBC report pointed out that many 2W OEMs present high-quality prototypes for certification but switch to cost-cutting measures during mass production.
The lack of rigorous post-certification checks further exacerbates this problem. A Rajasthan-based two-wheeler OEM, speaking off the record, explained, "The (testing) process lacks follow-through. Once certified, manufacturers face minimal scrutiny, allowing for deviations in production quality that go unchecked."
This view is echoed by experts from WRI India that The Core spoke with, who stressed that robust enforcement mechanisms, such as Confirmation of Production (COP) checks, are critical regulatory mechanisms for the Indian market context. These checks could ensure vehicles produced en masse adhere to the same safety and quality standards as the prototypes approved during certification.
According to the CTO of the EV manufacturer quoted earlier, "By introducing COP and mid-production checks, regulators are creating a safety net that reduces the chances of manufacturers cutting corners once certification is granted.”
Data from NITI Aayog projects India’s cumulative battery demand to reach 600 GWh by 2030. While initiatives like the PLI scheme for battery manufacturing and updated AIS standards signal progress, their implementation must be complemented by enhanced enforcement mechanisms. Without this, the industry risks repeating the same mistakes, undermining the potential of EVs to drive a cleaner, more sustainable future.
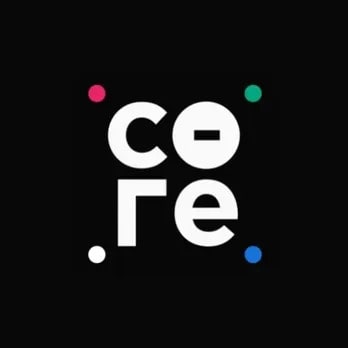
With over 1 million electric two-wheelers sold in India in 2024, the sector is booming. But beneath this growth lies a pressing concern—safety