
Location As A Strategy To Manage Manufacturing Costs Is Now Becoming History
While new US president Donald Trump’s plans of tariffs on imports into the US is a worry for businesses, the risk of tariffs always exists thanks to geopolitical scenarios.
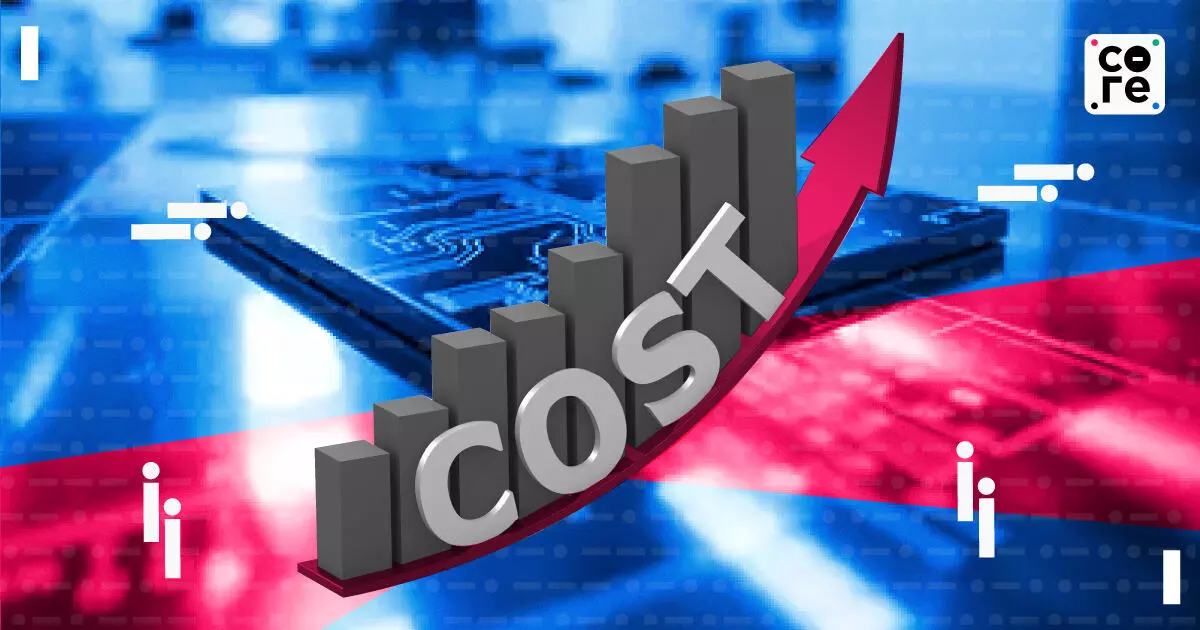
There was a time when business success meant making a great product and then selling it at a price that helped recover the costs of making the product and selling it — including advertising, marketing and distribution — and there were still profits on the table.
In the last few decades, profitability has been significantly dependent on where you produce a product rather than on where and how you sell it. Older Indian manufacturing companies are used to this, having moved production between different states hunting for the best tax incentives.
Locations like Silvassa, in the union territory of Dadra and Nagar Haveli adjoining Gujarat, Pantnagar in Himachal Pradesh and Haridwar in Uttarakhand were well known for this. In the early 2000s, new industrial units set up in these areas could be entitled to a 100% corporate tax exemption for five years and roughly 30% taxes for the next five. In addition, they got a 100% excise duty exemption for 10 years from the date of commencement of commercial production. The excise duty part is now subsumed into the Goods & Service Tax as of 2017 and the tax holidays are over in any case.
Nevertheless, all these places still enjoy the benefits of industrialisation and job creation even if they are not logistically best positioned in the national or global supply chains, particularly Pant Nagar and Haridwar.
Location Shopping Moves Abroad
If location shopping was earlier c...
There was a time when business success meant making a great product and then selling it at a price that helped recover the costs of making the product and selling it — including advertising, marketing and distribution — and there were still profits on the table.
In the last few decades, profitability has been significantly dependent on where you produce a product rather than on where and how you sell it. Older Indian manufacturing companies are used to this, having moved production between different states hunting for the best tax incentives.
Locations like Silvassa, in the union territory of Dadra and Nagar Haveli adjoining Gujarat, Pantnagar in Himachal Pradesh and Haridwar in Uttarakhand were well known for this. In the early 2000s, new industrial units set up in these areas could be entitled to a 100% corporate tax exemption for five years and roughly 30% taxes for the next five. In addition, they got a 100% excise duty exemption for 10 years from the date of commencement of commercial production. The excise duty part is now subsumed into the Goods & Service Tax as of 2017 and the tax holidays are over in any case.
Nevertheless, all these places still enjoy the benefits of industrialisation and job creation even if they are not logistically best positioned in the national or global supply chains, particularly Pant Nagar and Haridwar.
Location Shopping Moves Abroad
If location shopping was earlier confined within India, it’s also gone global. For almost 20 years, major exporters in India’s garments industry have been moving production to Bangladesh with most of them hosting factories there, making garments from cotton and yarn often imported from India.
A report in Outlook Business says 25% of manufacturing units in Bangladesh are owned by Indian companies. This includes Shahi Exports, House of Pearl Fashions and Gokaldas Images. Indian companies have also been importing directly from China and in many cases, badging products here. White goods like air conditioners, toasters and electric irons are classic examples, where products are made in China but sold in India under a local brand.
Donald Trump's election as president of the United States and the real possibility of high tariffs — ranging from 20% to 60% — on imports into the US will put manufacturers the world over in a quandary. Firms making in China are bracing for the worst.
Shoe brand Steve Madden has said it will reduce goods manufactured in China by 40% within the next year, up from its prior target of a 10% reduction. “As of yesterday morning, we are putting that plan into motion,” chief executive officer Edward Rosenfeld told analysts on an earnings call Thursday reported by Bloomberg.
Whirlpool Corp., which makes Maytag and Amana household appliances, said Americans will see higher prices on microwaves if tariffs are increased. “The biggest thing we get out of China is microwaves,” a top official told Bloomberg just before the election but added that they would be more insulated from the risk than other manufacturers because it produces most of its goods sold in the US domestically.
Steve Madden said only under half of its current business would be potentially subject to tariffs on Chinese imports. If the company’s plan to mitigate its exposure is successful, that would drop to around 25% within the next year. That is because, like many others, the company has been shifting its supply chain more toward Cambodia, Vietnam, Mexico and other countries. Some years ago, 95% of Steve Madden’s imports came from China.
Locations Won’t Matter
Indian manufacturers are possibly better off staying at home and trying to produce more efficiently and hoping that if India faces tariffs, they are a lower band and that bilateral negotiations lead to some compromise. But for manufacturers and producers, the larger lesson is that location as a strategy to manage costs is now receding into history.
Even if the US relents, the uncertainty on tariffs linked to geopolitics will stay and most likely increase. Companies will have no choice but to produce closer to their consuming market.
Which puts manufacturers in a bind because producing in relatively higher-cost countries like India which have large markets will also push prices higher and make it less profitable, whether it is for the intermediate or final product.
That is a problem India has to solve at some point.
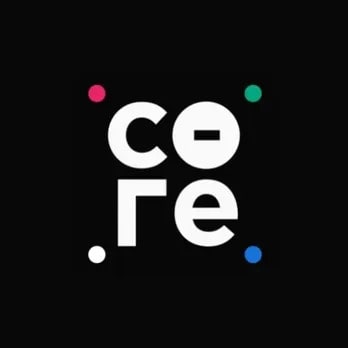
While new US president Donald Trump’s plans of tariffs on imports into the US is a worry for businesses, the risk of tariffs always exists thanks to geopolitical scenarios.