
India’s Aviation Industry Has A Problem: Its Top Engineers Are Moving Abroad
Despite India’s booming aviation sector, engineers are fleeing to international airlines for better pay and opportunities. Can new training centres change the game?
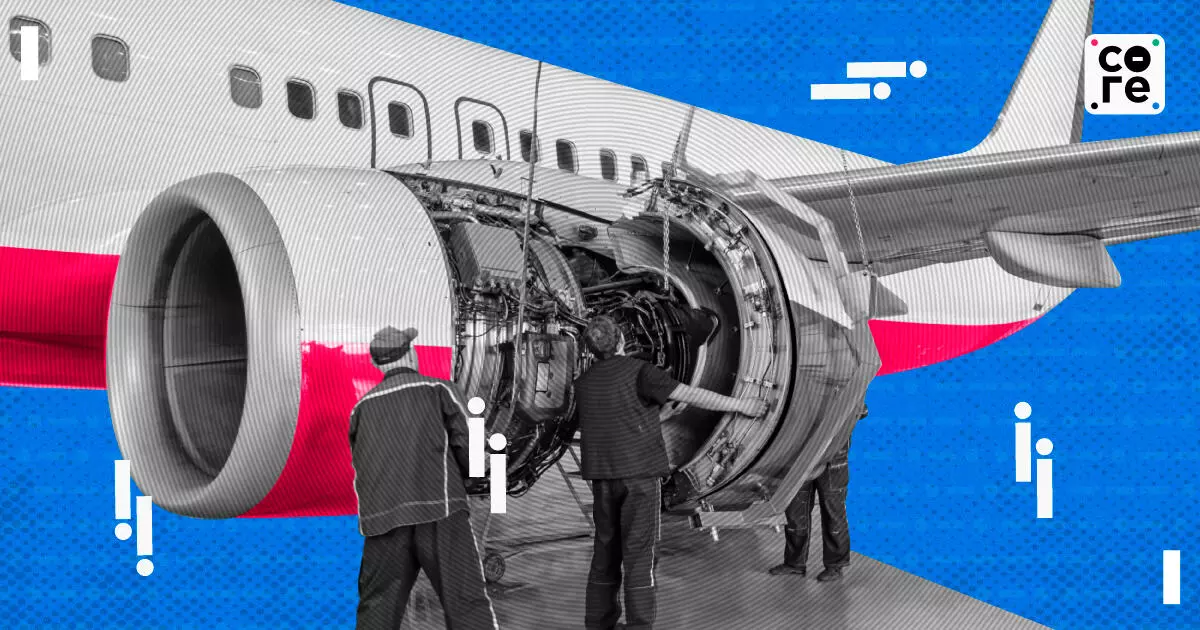
India’s maintenance, repair, and overhaul (MRO) industry meant for aviation isn’t in good shape. But now it desperately needs a makeover as Indian airlines expand their fleet.
With Air India and IndiGo going all out, ordering a fleet of wide-body and narrow-body aircraft to meet surging passenger and cargo demand, the aviation industry has been pushing for homegrown facilities. Tata-owned Air India plans to set up MRO centres across the country, aiming to cut down on outsourcing, which currently makes up a staggering 90% of our MRO work. It has already started construction of its MRO centre in Bengaluru.
But this isn’t going to happen as easily as it seems. India’s MRO sector faces many challenges, as The Core has reported earlier. There are problems with securing investments, getting inadequate infrastructure and high taxes.
Another pressing reason that India relies on foreign MROs is that our planes are leased, and lessors prefer sending them off to Singapore, Malaysia, Indonesia, and Europe for maintenance.
But as the aviation industry looks to set up more homegrown facilities, there’s one more problem that looms — the lack of skilled engineers in the country.
Industry experts pointed out a troubling trend — engineers trained in India are packing their bags and hea...
India’s maintenance, repair, and overhaul (MRO) industry meant for aviation isn’t in good shape. But now it desperately needs a makeover as Indian airlines expand their fleet.
With Air India and IndiGo going all out, ordering a fleet of wide-body and narrow-body aircraft to meet surging passenger and cargo demand, the aviation industry has been pushing for homegrown facilities. Tata-owned Air India plans to set up MRO centres across the country, aiming to cut down on outsourcing, which currently makes up a staggering 90% of our MRO work. It has already started construction of its MRO centre in Bengaluru.
But this isn’t going to happen as easily as it seems. India’s MRO sector faces many challenges, as The Core has reported earlier. There are problems with securing investments, getting inadequate infrastructure and high taxes.
Another pressing reason that India relies on foreign MROs is that our planes are leased, and lessors prefer sending them off to Singapore, Malaysia, Indonesia, and Europe for maintenance.
But as the aviation industry looks to set up more homegrown facilities, there’s one more problem that looms — the lack of skilled engineers in the country.
Industry experts pointed out a troubling trend — engineers trained in India are packing their bags and heading to Gulf countries for jobs. The reason? A better standard of living.
“There is a significant talent gap in India’s MRO sector. While India is the largest supplier of aviation talent to the Middle East and APAC regions, domestic MRO operators struggle to retain skilled professionals. The government needs to intervene and enforce regulations to protect and promote this industry,” Pulak Sen, founder of the MRO Association of India told The Core.
So, while we’re expanding our fleet, are we also doing enough to keep our talent? That’s the real turbulence India’s MRO sector needs to tackle.
Why Are Engineers Leaving?
It is no secret that about 30% of Indian students who complete aviation courses domestically end up working for international airlines. While India has ramped up its efforts in skill development, it’s hard to compete with the salaries offered abroad.
For instance, a fresh graduate working for Indian authorities may earn Rs 1 lakh for an eight to ten-hour shift, but the same job in Dubai offers nearly double the pay. India's lower wages are due to the outsourcing of heavy-duty MRO tasks, leading to less work and smaller pay packages.
“This disparity drives many to seek opportunities in the Gulf countries. After five to six years of gaining experience abroad, these professionals often return to India, where their enhanced skills allow them to secure high-paying senior positions,” Subhajit Maity, accountable manager head at Thakur Institute of Aviation Technology told The Core.
This trend has been growing especially post-pandemic, with many engineers opting for international roles with higher pay scales, only to return later to better-paying domestic jobs. With international experience and high salaries, they qualify for senior roles upon return.
Although India’s MRO industry is expected to double from US $2 billion to US $4 billion in the next seven years, today about 90% of the heavy maintenance work is outsourced, leading to lower profit margins for domestic companies.
“Our manpower might be the cheapest around, but that doesn’t translate to high profits as MROs here (in India) barely make 3% to 7% margins. Compare that to other countries, where fatter profits mean they can afford to pay their people better,” said Sen.
The Golden Days of MROs: A Look Back
Rewind to the 1980s, when India’s national carrier dominated MRO, then called Tata Airlines, now Air India. Back then, the focus was on self-reliance, with the airline handling all maintenance, repair, and overhaul tasks in-house at its base in Mumbai.
Aviation expert Sanjeet Rokat who was with Air India for 30+years under MRO told The Core about the industry's glory days.
“It was the era of doing everything in-house from aircraft maintenance, engine repairs, component servicing, you name it. The government encouraged the public sector to create jobs, so handling all this internally was the trend,” he shared.
Fast forward to today, and the landscape looks completely different, with the shift from local to foreign MRO starting in the 1990s. "By the 90s, when private players entered the scene, the focus shifted to cost efficiency, and MROs began outsourcing," Mark Martin, founder and CEO of Martin Consulting, told The Core.
With new technology and new engines coming in, airlines began to outsource most of their maintenance work, seeking efficiency and cost savings. “When you outsource, you get volumes, and volumes mean lower costs for maintenance and repair,” Rokat explained.
Talent Development: Is Training Enough?
In the earlier days, aviation engineers would join MRO facilities as trainees and gradually become full-time employees. Today, India's MRO training institutions include Thakur Institute of Aviation Technology, Flytech Aviation Academy, and GMR School of Aviation, to name a few.
The training process for an aircraft maintenance engineer spans over four years, including theoretical and practical lessons.
“Only institutes offering DGCA-approved aircraft maintenance engineering courses can prepare students for airline jobs. The course spans 2400 hours over 2.5 years, plus 1.5 years of training,” Maity explained.
Institutions like Thakur Institute have partnerships with airlines like IndiGo and AIESL to offer live aircraft training.
"Our institute was the first in India to receive European Union Aviation Safety Agency (EASA) approval in 2015. Since then, we have consistently hosted international students from Bhutan, Bangladesh, and Gulf countries,” Maity added.
Can New Training Centers Solve the Problem?
Air India is actively setting up MRO centres and training institutes across India, including a mega MRO facility in Bengaluru and a training institute in Amravati, Maharashtra, scheduled to open by 2026.
Despite these efforts, retaining talent in India remains a challenge. Earlier this year, Air India announced a collaboration with Singapore-based SIA Engineering Company (SIAEC) to establish a base maintenance facility in Bengaluru, a step toward building a self-reliant aviation ecosystem.
Yet, as Sen pointed out, “New training centres are great, but the poor salary structure makes it hard to keep talent from flying away.”
Other airlines, like IndiGo and Akasa Air, have also ramped up their recruitment and training efforts. However, the fundamental issue remains the pay gap between domestic and international opportunities.
At the Thakur Institute of Aviation Technology, campus recruitment efforts from companies like IndiGo, Vistara and SpiceJet offer stipends of Rs 25,000 to Rs 50,000 during training, with post-training salaries ranging from Rs 1 lakh to Rs 1.5 lakh per month for domestic positions.
In comparison, international graduates can earn starting salaries of Rs 2.25 lakh abroad, making it difficult for Indian companies to retain talent.
The Impact on India’s Aviation Industry
The global aviation industry, severely impacted by the Covid-19 pandemic, is now bouncing back. India’s aviation sector is growing rapidly, with airlines like Air India and IndiGo expanding their fleets. This growth has led to a greater demand for skilled technicians, pilots, and engineers, a demand that India is struggling to meet.
Many Indian engineers are opting to work for international airlines, further exacerbating the shortage of skilled personnel in India.
“We are facing a brain drain. A decent engineer wouldn’t dream of staying in India when they can earn significantly more with a Gulf carrier. We need strong government intervention to overhaul everything and address this talent gap,” Martin said.
The challenge lies in creating enough high-quality training centres and offering competitive salaries to prevent Indian engineers from leaving the country.
An engineer in the Middle East can earn up to 4-6 times higher than what their Indian peers make. It is no wonder many people move out of India and the pay gap alone is enough to fuel this brain drain.
India’s aviation industry stands at a critical juncture. Sure, we are making moves by building MRO centres and ramping up training programs, but unless we close that glaring wage gap, we’ll keep losing our top talent.
What’s needed? A full-blown strategy with government backing, competitive salaries, and better training if we want a thriving aviation ecosystem at home.
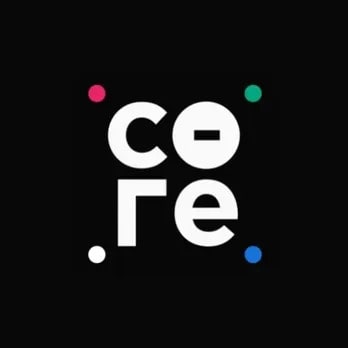
Despite India’s booming aviation sector, engineers are fleeing to international airlines for better pay and opportunities. Can new training centres change the game?