
India Can Become Global Green Energy Hub, Says Energy Expert Naveen Ahlawat
The push towards decarbonisation aims to position India as a global hub for green technology manufacturing and exports.
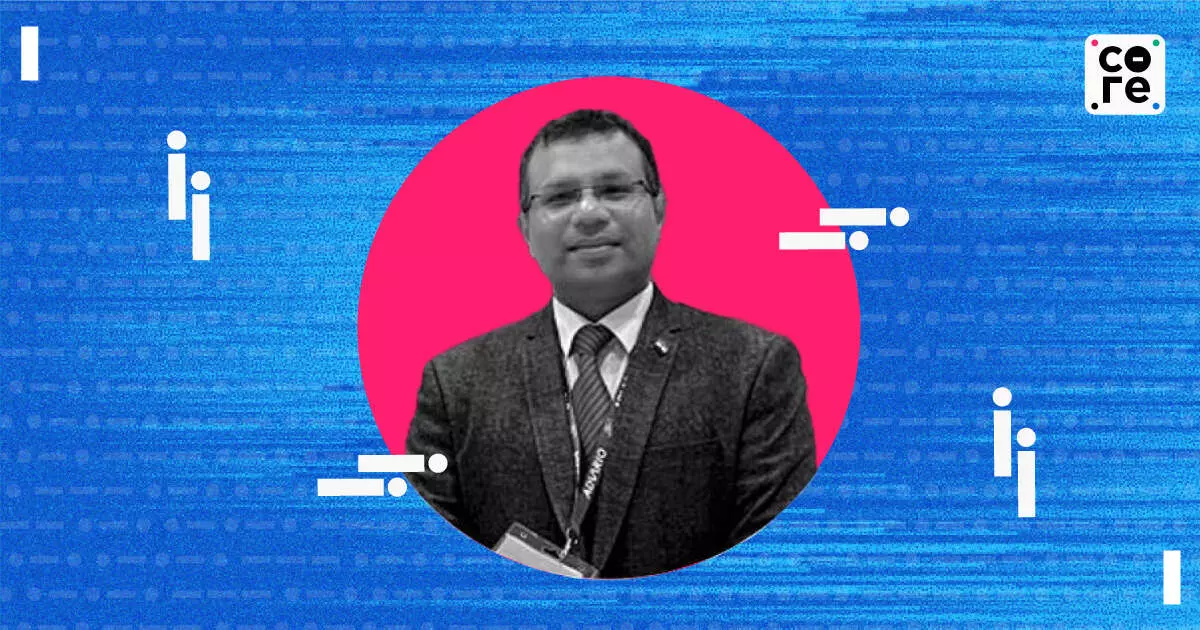
While globally the focus on shifting towards cleaner forms of energy is getting stronger by the day, India is in the middle of a significant transformation in the renewable energy space, with the potential to lead in the production and export of green energy.
“There is a good opportunity, and India stands a very good chance to seize this opportunity. It also gives a very good business case for India to really export, make electrolysers in India, make green ammonia in India, and then export green methanol,” Naveen Ahlawat, head of green hydrogen, green steel, gasification projects, and CCSU at Jindal Steel & Power Ltd, told The Core.
The push towards decarbonisation aims to achieve net-zero emissions by 2070 and position India as a global hub for green technology manufacturing and exports. According to Ahlawat, the future holds promising and disruptive opportunities that could pave the way for impactful advancements in India's renewable energy landscape.
Ahlawat said that the government is heavily investing in renewable energy. Efforts are underway to boost domestic production of solar PV modules, reducing reliance on imports from China and fostering a self-sufficient ecosystem.
“I think there are a lot of efforts being given by the government. There's a dedicated ministry vertical that has been formed like the Ministry of New Energy and Renewable Energy. The function of this ministry is to facilitat...
While globally the focus on shifting towards cleaner forms of energy is getting stronger by the day, India is in the middle of a significant transformation in the renewable energy space, with the potential to lead in the production and export of green energy.
“There is a good opportunity, and India stands a very good chance to seize this opportunity. It also gives a very good business case for India to really export, make electrolysers in India, make green ammonia in India, and then export green methanol,” Naveen Ahlawat, head of green hydrogen, green steel, gasification projects, and CCSU at Jindal Steel & Power Ltd, told The Core.
The push towards decarbonisation aims to achieve net-zero emissions by 2070 and position India as a global hub for green technology manufacturing and exports. According to Ahlawat, the future holds promising and disruptive opportunities that could pave the way for impactful advancements in India's renewable energy landscape.
Ahlawat said that the government is heavily investing in renewable energy. Efforts are underway to boost domestic production of solar PV modules, reducing reliance on imports from China and fostering a self-sufficient ecosystem.
“I think there are a lot of efforts being given by the government. There's a dedicated ministry vertical that has been formed like the Ministry of New Energy and Renewable Energy. The function of this ministry is to facilitate or to bring that interfacing between the industry and all the support and the off-takers (buyers),” Ahlawat said.
In The Core Report: Weekend Edition, financial journalist Govindraj Ethiraj spoke with Ahlawat to understand the changing energy space in India.
What are hydrogen and green hydrogen and why are we talking about it so much nowadays?
I think hydrogen, we are discussing because we believe, especially for ‘Hard to Abate’ industries like steel, aluminum, and cement, I think these industries can be decarbonised with hydrogen as the vector. It is very simple. Instead of using carbon, which eventually leads to carbon dioxide, we have to replace that carbon with hydrogen as one of the reductants in these industries.
Now hydrogen can act as a reductant for reducing iron ore to reduce iron, for the steel industry. Hydrogen, when used for aluminum or in cement, can act as an energy carrier. So hydrogen has both chemical properties, molecule properties for reductants, and energy carriers. That's why across the world, I think people have got traction toward hydrogen because, of these properties. And also this is basically one of the levers that can be utilised across the industry to accelerate decarbonisation.
I'm going to come to steel as an example. Now, steel production accounts for about 8% of global emissions which is why we want to bring hydrogen into the process. But now can you go back and say, how are we making steel today and how is the use of hydrogen or the potential of use of hydrogen, how could that change things?
Steel, as you rightly said, contributes close to 8 to 9% of the global green emissions across the world. Now it is very important to understand that if you talk about the overall contribution of steel in the global GDP (gross domestic product), it is close to 0.8% (point eight). But the contribution to the overall carbon intensity or greenhouse emission, is close to 8 to 9%, as you rightly said. It's close to ten odd times. That's why it is pertinent and it is paramount that we have to start taking these sectors to start basically accelerating the decarbonization process.
About 70% of the steel being manufactured today, is through blast furnaces, conventional blast furnaces, and basic oxygen furnaces right across the world. About 22% of the steel, is being manufactured via scrap-based recycled electric arc furnace route. The remaining 8%-9% is through the Direct Reduced Iron–DRI process, DRI electric arc furnace process. Now these are the three routes.
Now, if you try to understand that, how we can accelerate this decarbonisation. Now 70% is through conventional blast furnaces and BUF processors. And it is not easy to decarbonise that — because the blast furnaces historically have been built for 30-35 years. We haven't come across new technologies, that we are exploring or evaluating, where we can replace. We can replace the coal with hydrogen. Because hydrogen is an endothermic reaction. It brings cooling. When it takes heat or an endothermic process, it brings the overall temperature down in the blast furnace. That's why up to 5%, or 10%, we can inject the hydrogen in a blast furnace, but we cannot do it at a 100% level. That's where it calls for a technology disruption or it calls for a technological innovation that we all have been exploring.
What happens in a blast furnace today? And as I understand from what you're saying, the technology has not really changed for many decades now.
The process is very simple. To make one tonne of steel in the blast furnace, we add close to 1.8 tonnes of iron ore in the form of a lump or the form of a sinter plant — sintered particles. And along with that, we add close to 300 to 400 kgs of coking coal. This is the basic ingredient. Now, iron ore is typically required because that is a reduction. You have to take out the oxygen from the iron ore because it's a mix. It's an oxide form, iron oxide. That will act as a metallic, pure metallic for further processing, for further refining in the process.
In the blast furnace, what typically happens, is we make crude steel, only crude steel. Why do we say crude steel? Iron ore reacts with coking coal. It's the same reaction. Coking coal—you have carbon in this. This carbon takes the oxygen in the oxide form along with iron and forms the carbon dioxide. It's that the reaction goes like this. Carbon will take the oxygen from the iron oxide and it forms carbon monoxide (CO) and iron. So that iron has got silicon into this, it has got a little bit of phosphorus into it. That will be further refined in the downstream process.
That is in the basic oxygen furnace process.
And you're saying that ratio is 1: 300, 1 tonne of iron ore plus 300 tonnes of coking coal or coal?
Yes, to make one ton of crude steel we have to basically add 1.8 tonnes of iron ore and close to 300 to 400 kgs of coking coal. That is the overall process. The carbon dioxide that is coming out from the blast furnace, is the cause of all these problems.
If you want to bring in hydrogen in any significant way, then the entire technology has to change, which takes into the issue of costs, because you're effectively replacing a part or a good part of your steel plant that exists today. Is that correct?
Absolutely. The technology is already there. On the brass furnace level, these are the levers. But we have got the technologies. Now, if you talk about direct reduced iron, the DRI process, which is also one of the routes to manufacture steel, is the technology that we are adopting and that is a future-ready technology.
Now, what is happening in the existing DRI furnaces? We are using synthesis gas. The synthesis gas is a combination of hydrogen and carbon monoxide. And this hydrogen plus carbon monoxide can be derived through different routes. Again, we can make this synthesis gas from natural gas in Middle East areas like Oman, UAE, Qatar, and Saudi Arabia, where they have ample abundant reserves of natural gas.
In India as well?
In India, not much. We are net importers of natural gas. We don't have much natural gas resources, much less natural gas reserves. However, there is a plant being run by Arcelor Mittal, Nippon Steel now in Surat. They are importing natural gas plus they are also using a little bit of natural gas from India but it's a combination.
This, I thought, was the original Essar plant.
This was the original Essar plant but again, due to the paucity of natural gas, they used to import natural gas and that was one of the reasons why the cost of production was so high. Your landed price once it lands in India will come to the level of $7 to $8 per MMBtu, which is pretty high, as compared to these Middle Eastern countries where the spot price is between one to four dollars per MMBtu, almost half. And that helped them to reduce their cost of production. This is the idea of using natural gas, especially in these countries, and converting this natural gas into synthesis gas.
Second, our company, Jindal Steel Power, we are operating the world's only coal gasification-based DRI plant. We are gasifying coal, which is abundantly available in our country. We are the fourth largest, and we have the fourth-largest proven reserves of coal. We gasify that coal and make synthesis gas, and that gas we put into the DRI furnace. These are the two ways which are being utilised.
Now, what is going to change here? Nothing is going to change here. The only thing that is going to change is that we will keep on reducing this synthesis gas because it's a combination of hydrogen (H2) plus CO. Hydrogen eventually is going to strip that oxygen combined with iron ore, will form water and carbon dioxide (CO2)will also act as a reductant and strip that oxygen to form CO2. If this combination of H2 plus CO, if I can only limit myself to hydrogen and and remove CO, then I am through. Then the reaction will be exactly the same as what is going to happen in the blast furnace. Iron oxide will react with hydrogen to make iron and water. In that case, there won't be any carbon intensity.
So what is the way forward now? The way forward will be that the synthesis gas is a good enabler, it is a good backup. Plants are being run there. And the carbon intensity of all these plants is pretty low as compared to the conventional blast furnace route. The idea is to now get the green hydrogen maybe at the right time. Right now in India, the price is pretty high because of renewable energy. Prices are so high now, that maybe in the next two to three odd years or four years, when the renewable cost will come down, because of the cost of capital coming down, and the capex, it is already in the downtrend. When we reach a level of 1 to 2 cents (US cents) per kilowatt hour, that is a period when we can start adopting, we can start changing those electrons into molecules that are green hydrogen. And that's a sweet spot for all the industries. You talk about steel, you talk about aluminum, you talk about cement, for all these sectors, the sweet spot where they can start adopting green hydrogen in their processes is between $1 to $1.5 per kilograme. That's the sweet spot.
When we talk about hydrogen and green hydrogen, how are we making it? Where are we making it? And it's something that's not easy or cheap to make. Why is that?
The hydrogen that is being used now, hydrogen is not a new molecule. In fertilizer in refineries and petrochemical plants, hydrogen is being used for hydrogenation. The only source is that we are reforming the natural gas, or naphtha, to make this hydrogen. And that's why the color of that hydrogen is grey/black. Now, because of the carbon intensity to make one kilogramme of hydrogen via this route of naphtha or natural gas, it emits 12 kgs of CO2 into the atmosphere. That's why it is highly carbon intensive. And so many emissions are happening. Now to convert that into blue hydrogen — blue hydrogen is the CO2 that is going into this process of steam, typical steam methane reforming process, SMR routes. Instead of pushing the CO2 into the atmosphere, you capture that CO2 and sequester that CO2 under the ground or use that CO2 for enhanced oil recovery. In that case, the carbon intensity will come down from 11 to 12 kgs to 2-odd kgs. That's why the colour of the hydrogen that is being produced by this process is called blue hydrogen.
Coming to green hydrogen. Green hydrogen is a typical, basically hydrogen that is being produced by electrolysis process. In the electrolysis process, all the electrolyzer cells, electrolytic cells, and the input is renewable power. When we use renewable power coming from solar or wind or energy storage like batteries, or basically from hydro—those electrons are renewable. They are from these different streams like solar, wind, and hydro. And those electrons will go into the electrolytic cell and convert that water. Water is going to be the input into that electrode cell. And it will convert into hydrogen and oxygen. And that hydrogen will take, if the pressure required for the hydrogen in some process, like in ammonia, green ammonia that is close to 120 bar gauge–140 bar gauge.
For steel manufacturing, like in DRI processes, the pressure is around eight to ten bar gauges. There, the compression required is much less. The hydrogen produced by electrolyte cells or the water electrolysis, is called green hydrogen because the electrons or the renewable power used to crack this water is renewable, it is green. And the hydrogen that is coming out from the electrolyte cell, is called green hydrogen that is being used.
And in terms of producing it today as we are in India, where are we, and where are we producing it? How viable is it looking? Where is it going?
I think in India there is no specific location. The idea is that there are different combinations. But one of the most, you know, basically reliable combinations is–in India, we have got a very robust distribution network of renewable power. I can produce renewable power, or I can put a wind farm down south in Karnataka and Tamil Nadu, or I can put a solar farm in Bikaner in Rajasthan and transmit or distribute those electrons, bring those electrons through this network to my plant and I can co-locate. I can co-locate the electrolyzers at my plant and I use the hydrogen. This is the right way because of the distribution network in India. You can put your renewable projects anywhere in India, bring those electrons, and co-locate the electrolyzers along with your plant, make hydrogen, and then use the hydrogen. This is probably the best way to use hydrogen. There is no specific location per se, but this is how it is being done in India.
In the Middle East, you know, it is slightly complicated in the sense that they don’t have as robust a distribution network as India. That’s why there are some projects where they put the electrolyzer along with the solar or wind farm. The renewable energy generated in those farms is directly fed into the electrolyzers, makes hydrogen, and then transmits that molecule to 10 to 15 to 25 to 40 km with the help of compressors. These are the different models. But in India, because of these enablers, because of this advantage, we have got a good support system from hydropower, from nuclear as well. That makes our transition much better. We are much better placed than any other country in the world.
As we stand in India today, there are a lot of efforts going on in the context of green hydrogen. Green steel and the new, as you mentioned, green cement. I can see how it's all coming together. What's going on right now, whether it's efforts by the government or private sector, and where could it be going in, let's say the next year or two?
I think there are a lot of efforts and a lot of support being given by the government and through the different levels. There's a dedicated ministry vertical that has been formed like the Ministry of New Energy and Renewable Energy. It's a new ministry that has been carved out. The function of this ministry is to facilitate or to bring that interfacing between the industry and all the support and the off-takers. Like the Ministry of New And Renewable Energy, what they normally do is tell us that, okay, your strength is in manufacturing steel. You focus on steel, you give your requirement for green hydrogen. We will get all the developers, and we will tell them to develop this product for you. And then you can be the off-taker, you can sign up long term, the way we sign the power purchase agreement, we can sign up long term hydrogen supply over the fence hydrogen take or pay contract with these guys. That's a huge support. It is all this integration because everything is new. Especially for the steel industry, though we are using hydrogen in the form of syngas. For us, the transition is from 52% to 100%. But still for the other companies where they are focusing or maximising the BF and BUF route, for them handling this molecule is not so easy. That's why you need other actors who can, or other anchor players who can support you in this journey. Let them basically get you the green hydrogen over the fence and then you can do the downstream processing.
Second, we are now talking from 0 to 100. Today we are black or grey and then green. This is like 0 to 100. But there is also a play, that is the interim play where because we are talking about this transition, we are not talking about transformation. This transition can only happen through different or other entry routes using blue, like blue synthesis gas, and blue hydrogen.
The government is also promoting coal gasification as one of the routes. Because as I told you earlier, we have the largest reserves of coal. If we can monetise or create a different revenue stream of this coal, to convert this coal into synthesis gas and use that gas in our DRI processes, that also is one of the good possible options for transition.
The government is planning to gasify 100 million tonnes of coal by 2030. And they have come up with a lot of schemes, and viability gap funding schemes and they want to order award these projects within the next year. There is a lot of traction. This is on the coal gasification side, on the green hydrogen side.
And then on the renewable side, there is so much being talked about, the putting of the solar form, making the modules, the PV modules in India, the approved list of modules manufacturers — the government has approved so that we can manufacture all these model in the house in India so that we can create this entire ecosystem.
Right now, 90% of this stuff is coming from China. All these, I think, support the system that is being created. And there will be so much emphasis, I think after June 4. I think once we have the government in place, there will be so much emphasis on green hydrogen, green ammonia, and renewable power. And renewable power—solar and wind, I think, we have more or less come to maturity in terms of the learning, in terms of the after-sales services, in terms of the overall human capital that is required. I think now the focus will be more on the storage part, and how we store it.
There's so much emphasis being put on nuclear as well. I think the government sees this fact that we can be. There is a good opportunity, and India stands a very good chance to seize this opportunity. And there is a first thing that will help in your decarbonisation process to achieve our net zero by 2070. Second, it also gives a very good business case for India to really export, make electrolyzers in India, make green ammonia in India, and then export green methanol.
I see very impactful and disruptive times ahead and a very good opportunity for India to seize this opportunity.
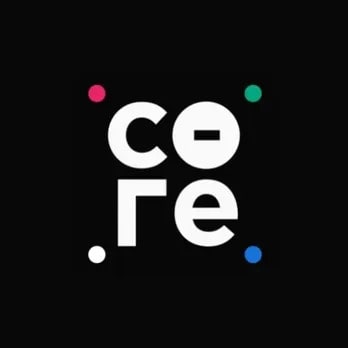
The push towards decarbonisation aims to position India as a global hub for green technology manufacturing and exports.