
‘Golden Opportunity': Hindalco MD Satish Pai On What China Plus One Could Do For Indian Manufacturing
For The Core Report: Weekend Edition, Pai spoke to financial journalist Govindraj Ethiraj on the company's core business and how it is now evolving.
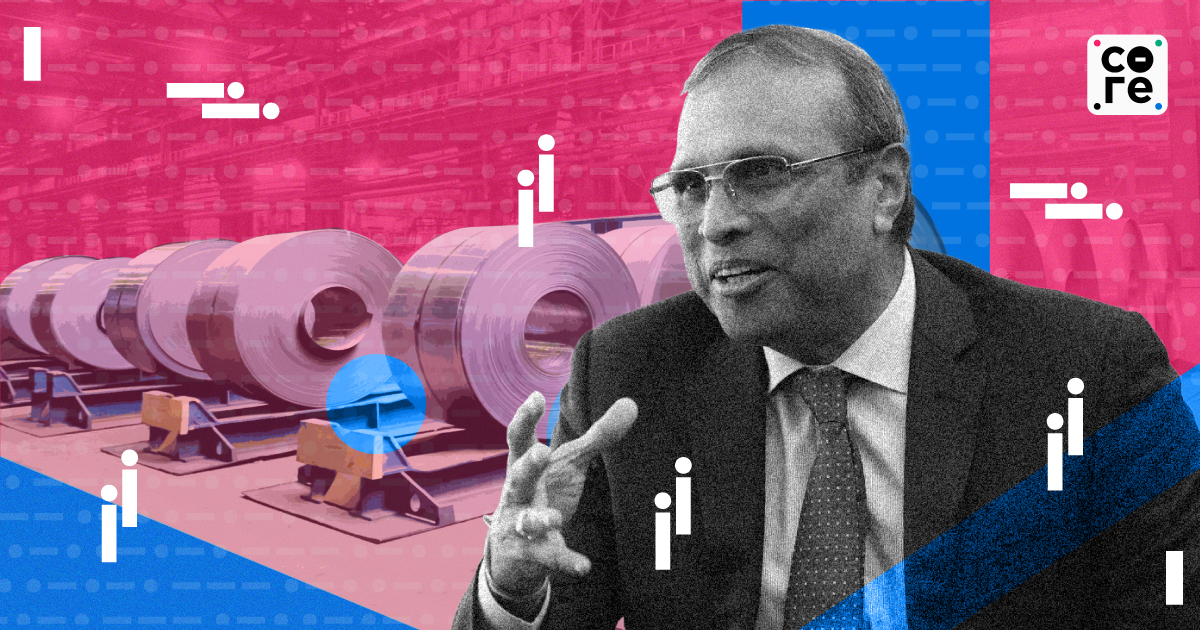
The Covid-19 pandemic was a lesson in crisis management. It negatively impacted the logistics industry the world over. India Inc had to rudely wake up to the importance of logistics. Not just procurement, but logistics has now become core to manufacturing.
The pandemic also made Indian companies better at responding to any kind of external instability. Had the Russia-Ukraine war and the ongoing crisis between Israel and Palestine happened before Covid, India Inc?s response to them would have been much different from what it has been now, Satish Pai, managing director of Hindalco Industries, told The Core.
?I think what has happened is that companies, countries, post-Covid have become in some ways very competent in what I would call crisis management. Nowadays, if a crisis happens, people are prepared? they don't nervously react. I think the world post-Covid is a lot more tuned to crisis management. As companies now, we don't panic very easily,? he said.
Hindalco is the largest provider of aluminium sheets to the auto industry globally. Pai said that according to Hindalco?s contracts, 90% of them are for electric vehicles and less than 10 are for IC (internal combustion) engines (ICE).
?It's been amazing that in a very short period of time, two to three years, the majority of our aluminium now goes to electric vehicles. And why? Because the battery is so heav...
The Covid-19 pandemic was a lesson in crisis management. It negatively impacted the logistics industry the world over. India Inc had to rudely wake up to the importance of logistics. Not just procurement, but logistics has now become core to manufacturing.
The pandemic also made Indian companies better at responding to any kind of external instability. Had the Russia-Ukraine war and the ongoing crisis between Israel and Palestine happened before Covid, India Inc’s response to them would have been much different from what it has been now, Satish Pai, managing director of Hindalco Industries, told The Core.
“I think what has happened is that companies, countries, post-Covid have become in some ways very competent in what I would call crisis management. Nowadays, if a crisis happens, people are prepared… they don't nervously react. I think the world post-Covid is a lot more tuned to crisis management. As companies now, we don't panic very easily,” he said.
Hindalco is the largest provider of aluminium sheets to the auto industry globally. Pai said that according to Hindalco’s contracts, 90% of them are for electric vehicles and less than 10 are for IC (internal combustion) engines (ICE).
“It's been amazing that in a very short period of time, two to three years, the majority of our aluminium now goes to electric vehicles. And why? Because the battery is so heavy people don't realise a battery vehicle of the same size of an ICE weighs 25% more. Everybody's trying to lightweight to get that 25% back. More aluminium, more than double of what goes into ICE engines goes in an EV-based automobile,” he said.
For The Core Report: Weekend Edition, Pai spoke to financial journalist Govindraj Ethiraj on the company’s core business and how it is now evolving.
Edited excerpts:
Hindalco is in the business of aluminium, copper, alumina, which is an input into making aluminium. Can you tell us from a broader trends perspective first, what is happening right now in the metal space and aluminium and copper in specific?
We are in very interesting times because both aluminium and copper theoretically are metals that can play and are playing a big role in the whole decarbonisation of the economy, in the sense that whether it's electrification of cars, or batteries or solar panels. You will find that aluminium and copper are widely used. And hence every analyst's long term demand for this metal shows that the supply and demand is going to be very tight and we need to find ways of making more aluminium and copper.
But the real issue is that (whether) the current short-term (weakness) is because of various macroeconomic issues that are happening, which is whether it's a weakness in the European markets, whether it's the Chinese economy slowing down, the demand for the metal is quite low. We are in this place where commodity prices for aluminium and copper are quite weak, but at the same time, everybody's saying that the future is going to be great.
I was talking to someone in the copper space and they were saying that in the last few years, one of the biggest surprises was the way the electric vehicle industry started consuming copper. And the sheer amount of copper and aluminium that goes into a vehicle versus what would be used in an electric vehicle. Tell us from your perspective as the supplier of this, how things have changed maybe in the last five years, and also the sort of composition of clientele, so to speak.
I'll tell you the interesting point here. We are the largest provider of aluminium sheet to the auto industry.
When you say largest, you mean in India or India plus world?
Worldwide. In India actually there's hardly any aluminium used. Through our subsidiary Novelis, we are the largest. When we actually started out five years ago, it was driven by the CAFE (Corporate Average Fuel Economy or Efficiency) regulations in the US to reduce emissions. Which is why they were trying to lightweight the cars and the big super heavy duty F-150s and all—they were using aluminium. That was the driver.
Now, when I sign our internal contracts, 90% of them are for electric vehicles and less than 10 are for IC (internal combustion) engines (ICE). It's been amazing that in a very short period of time, two to three years, the majority of our aluminium now goes to electric vehicles. And why? Because the battery is so heavy that people don't realise a battery vehicle of the same size of an ICE weighs 25% more. Everybody's trying to lightweight to get that 25% back. More aluminium, more than double of what goes into ICE engines goes in an EV-based automobile.
From a client composition, how much was EV, let's say six or seven years ago, versus what it is today? Or let's say before EV came in?
Before EV came in, then 99.9% of our customers on the auto side were conventional auto companies. And if you look at the market end, solar panel makers were not a market for us. The battery, a lithium ion battery, uses copper foil and aluminium foil as a cathode and anode. None of these customers existed at that time. We were, I think, 80% cans, beverage cans, which have been there for a long time, and housing—facades, doors, windows. But suddenly today, if you look at it, more than 20% of our market is autos, primarily driven by electric vehicles. And then all these solar panel makers and all are starting to use more and more aluminium extrusions and all that. It's quite amazing how the client profile for us has dramatically changed.
So you're saying 20% of the aluminium, the final product that you sell, goes to the auto sector?
Auto sector.
And the other 80%?
(About) 60% going to beverage packaging, largely cans, and then a large part is going to industries. I mean, all white goods, all computers, all high end phones, all multistoried buildings, facades, it's all aluminium.
And what's changing in this in terms of the way people are consuming the same metal or the types of metal?
I think there are a couple of things. One is the weight to strength ratio. Where aluminium plays off is one third the weight of a steel, but at the same time can be stronger. If you're going to do anything that requires strength and is light, then you're going to go for aluminium versus the conventional steel that they used to use. That is one very important driver.
The second thing is the look and the aesthetics. If you see, I don't know, an Apple phone or a computer, which has got an aluminium case because it's coated or anodised, the finish you can get… Very high end goods tend to go for aluminium as well. There are some of these things. And then the other part, which is quite amazing, is the recyclability of aluminium. You can recycle aluminium infinitely. In the current sustainability-driven environment, people are coming to aluminium because, like, take a can of Coke, you could be 90% recycled metal heading towards 100%. That also is one of the drivers. They're saying, okay, I'm using something which is made from recycled metal. Soon you will have a car that will be 100% recycled metal. That is a big demand these days.
Let's say, the 100 tons of aluminium you produce, how much of it is recycled and how much of it is, in an absolute sense, coming back to you.
I'll just take the Hindalco numbers. We roughly produce and ship about four and a half million tons of aluminium. And today, 2.3 million tons of aluminium is recycled. We are roughly 60% recycled today. Now, in cans, it's 85%. In autos, it's about 20-30%. We are working on how to recycle more in auto.
And how does economics work? I'm sure the collection and retrieval mechanism for cans is well established.
Yes.
Auto, maybe not so much.
Yes.
How does it work, the supply chain of that and the economics.
As you said, the supply chain for autos needs to be set up. There is a key difference. The life cycle of a can is less than three months… in the sense you produce it, you drink it, you discard it, it comes back to us and goes back. And (for) auto is on the road for 15 years. You have a different lifecycle that you're dealing with, but it's starting to happen.
Now you have auto companies that are designing for recycling. You have supply chains being set up. You have supply chains that are now handling segregated scrap, because in the olden days, they used to just squash the auto and then crush it. Now, you know, different alloys are used for different parts. They need to be separated. The whole circular economy and recycling is becoming a big supply chain exercise and a very high-tech exercise now, because you're dealing with alloys, you're dealing with segregation, you have separation technology. All that is a lot of investment is going into it now.
You said 4.5 million tons. Over what period is that?
No, every year we shift/ship 4.5 million tons.
How much raw material do you consume today for that? And how much were you consuming, let's say, before recycling reached the peak that it has.
The aluminium industry is divided into upstream and downstream. On the upstream side, we produce 1.3 million tons. On the downstream side, we ship 4.5 million tons.
To answer your question, if you go back in history, maybe 4.5 million tons, the amount of scrap we would use would be, I don't know, 1-2 lakh. Today we are 2.3 and that number is going up every year we're recycled. The demand for upstream primary, over time as a percentage is coming down.
And therefore the raw material that you would traditionally consume, that's aluminium being one of them, or Bauxite is coming down,
Is coming down.
How much less are you mining Bauxite today?
The funny thing that's happening is aluminium demand is growing at 4%, but there is no new aluminium smelting capacity coming up anywhere in the world. What the world is actually looking or working towards is that over time, the increase in demand will be met by recycling. This is the big decarbonization strategy of aluminium.
And does the plant itself at the manufacturing end change as you do more recycling versus, let's say, conversion of alumina to aluminium?
On the upstream side, the big driver, when you buy an ingot of aluminium, what you're buying is electricity, because 40%. is energy.
Is energy like steel?
Yeah. I don't know if steel is 40. I think steel is more like 20, maybe. Aluminium is a very electrolysis process, so it's very electricity intensive. What is really changing there is what is your source of electricity? Besides we can talk about efficiency, digital, which is completely changing how aluminium is made. The biggest pressure and the biggest change is on what we call how you can use more renewable power in the aluminium smelting process. And the key thing that is really critical there is storage. Because aluminium needs 365 days, very steady power, whereas solar works for 8 hours.
Wind can give you some backup over the evening, but what do you do in the night? Most people, like us, are experimenting with pump storage and other storage technologies to try to get an electricity source that's not fossil fuel or coal based. That's where most of the technology innovations are happening.
And the other one is digital. I mean, our Renukoot plant, which started in 1961, has 15,000 employees, makes about 400,000 tons of aluminium. One hour away is our state-of-the-art Mahan Smelter, which produces 365,000 tons and has 1,000 employees. That's the whole technology thing. I mean, newer plants today are very automated, very digital, and require less people, but more educated people.
You mentioned Renukoot. You also had a power plant. And precisely for the reason you mentioned that energy is a critical component. What's changing beyond what you said already? I'm assuming you want to bring energy costs down. You are also looking for alternative energy, and you're also trying to change the way you produce or more efficiently produce the metal. Between these three, where are you seeing the maximum progress at this point of time, from a technology point of view?
Two things are happening. The grid is becoming important. If you go back 25-30 years, everyone who put an aluminium smelter in India would build their own power plant because they wouldn't trust the grid. Now, what is happening is that the national grid is becoming critical. It's becoming more stable. The government is spending huge amounts of money expanding that grid. It's a national grid. For me, one big innovation is the grid. If we expand aluminium today, we would not put up any more captive power. We would take the power from the grid like most countries, advanced countries in the world do. That's one really big innovation.
The second big innovation, as I said, is what we call round-the-clock power. How can I get from the grid, which is 80-85% load factor? Somebody is putting together for you a combination of solar, wind, pump storage, thermal, and giving you as a user power, which you can then say is 75% zero carbon. It's a huge technology innovation that needs to happen there for you to get that what I call round-the-clock power. We are the ones who signed the first one, and we are hoping by the end of next year, we will start to get power from the grid that way.
Currently, the power that you generate in Renukoot, for example, is entirely…
It's captive
And thermal.
Yes.
How many megawatts is that? Second, what's the megawatt to per ton of aluminium equation?
It's 13,500 kilowatts per ton of aluminium. I'm just taking a general average. Now, if you take Mahan or Renukoot, we are producing roughly 650 thermal in each place captive. We are now starting to inject from the grid. Once these RTC contracts come in, we are going to start with 100 megawatts at a time.
Yeah. And when you talked about energy, I mean, 650 megawatt can power a small town.
Yes.
That's the kind of energy that you're consuming of this. Now, what's the balancing that's going to likely to happen as you bring in, as you said, more solar or pump storage or so on.
Our target, which we have committed to is by 2030, 30% of our power will be green. That means I can have 70% thermal, 30% green, a combination of green, which is solar, wind and pump storage.
And the technology part, which I guess people call the Industry 4.0. What is it trying to do or doing in your own factory? One is, I'm assuming, managing energy, because that's a critical part. What are the other things that it's doing? And even within managing energy, how is it doing it?
A manufacturing business, when you look at it, what are we trying to do? We run 24 x 7, three shifts. You're trying to get machines to run at a very stable operational level with the best efficiencies 24 x 7 and 365 days. That's what manufacturing is.
What Industry 4.0 or digital is trying to do is to keep your uptime at the maximum levels, reduce your unplanned downtimes, make your power and your efficiency factors as good as they can. Because in our business, the lowest cost producer is the last man standing. That's basically digital. That's what we are trying to do because whenever you have human beings, you have errors, you have unplanned downtimes, you have breakdowns that you didn't do. What we are trying to do is to get automation, artificial intelligence, predictive maintenance, all that to get the uptime as high as possible.
What are the key sensors and what are they sensing in an aluminium production process at this point? What's the key thing that you want to know, or what are the key things that you want to know and are monitoring, which you are able to do better today than maybe earlier, before 4.0 came in?
What has happened is that machines you are now measuring their temperature, their vibration, things that before people would ... The real experienced guys would say: Mein awazz sunke bol sakta hoon kuch kharab ho raha hain. You were dependent on that. Today you're getting 24 x 7 vibration reports, temperature reports. You're getting cameras that are watching the product come out. Before, somebody had to look at it with the eye. Now camera scanning is doing that. All these things are what are really making a step change in terms of quality and performance.
The idea is that you, from the vibration pattern, can see that a motor is going to fail, so you stop it beforehand and take care of it so that you don't have an unplanned downtime.
And on energy between India and, let's say, Alabama, in the United States, I mean, how different is it in terms of the cost per ton of aluminium produced today?
Actually, in India, we are in Hindalco, probably one of the lowest cost per ton, because the cost of power in the Western world is much higher than in India. Now, it's also true that because we are heavily coal-based, our prices are low. That's a reality. But compared to the Western world, our costs are much lower. It's compared to China that we struggle with, because China's power is subsidised. They are also heavily coal based. My biggest competitors are in Canada, in Norway, and they have 20-25 year hydro contracts, because their most power in Norway and Canada is hydropower. And that is my biggest problem, because they are green and they have a very low cost of operations. Once they set up the dam, they get power at very low cost. That's our biggest competition today.
And because they're green, does that mean that investors also look at them more kindly?
Yes, yes. Though it's very interesting, the Dow Jones Sustainability Index ranks Hindalco as the most sustainable aluminium company, better than (Norsk) Hydro and Alcoa. And why? Because even though our power comes from coal, we are much better at waste management. We are much better at water management, we are much better at biodiversity because in India, these things are very important, whereas in the Western world, they have not started to focus a lot on water, waste management yet, as much as we have. Like, for example, Hindalco, 80% of all waste produced does not go to landfills, it's recycled, which is quite remarkable.
And I've asked you about aluminium all this while. Tell us about copper and the similar question first. I mean, what are the trends that you're seeing right now?
Copper, the interesting thing is the amount of wiring. If you actually sit in an EV now, besides the battery, most of your weight is coming from electronics and wiring. The copper demand is going to shoot through the roof. The problem with copper is that the copper ore itself, in India, we have very little. Bauxite, by the way, has the fourth highest reserves in the world. And where copper reserves are, which is basically South America, Australia or very hostile parts of Africa, the amount of concentrate that's available is getting less and less, whereas the demand for copper is going to go up. Again, there you're going to see a big squeeze because there is no concentrate. And hence we are also going down the copper recycling route because every electronic gadget you throw out needs to get recycled to get copper back.
Copper recycling rates are much lower than aluminium today. But I think that in the future, this concept of what we call urban mining is going to happen. We are going to set up a hundred thousand ton copper recycling facility in India as well.
But copper in general, smelting is something that attracts a lot of, let's say, environmental attention.
Yes, chemically, very complex, very polluting.
How do you see that in the mid to longer term?
I think that the fact that it is complex does not mean that you should not do it. There is enough technology to make sure that you do complex things in a clean and sustainable way. I mean, in our Dahej plant, we have spent huge amounts of money trying to get it to be very clean and sustainable. What it means is that the price of copper is going to go up, because if you want more copper and it has to be done the proper way, the cost of production is going to go up, and hence the price of copper is going to go up.
And how is that playing out right now?
Right now, you see, just about two-three years ago, the price of copper was $4,000-5,000 a ton. Today it's 8,000. And the predictions in the market are it's going to be between $12-15,000 a ton.
But you're saying this is also because suppliers are forced to increase prices, not just the demand factors which are playing.
The demand is going up. The supply is constrained, the ore and the mines are not that easily available. And the copper process itself is, as you said, very technically and chemically complex. The costs of making clean, green copper is going to go up.
And how much is, again, just a broader question between aluminium and copper: what's the split in Hindalco?
As I told you, we ship about 4.5 of aluminium and about half a million tons of copper.
And top line contribution?
Well, the top line is a bit misleading because, as I told you, the price of copper is very high. Copper is nearly 30- 40% of the top line, because the price of copper is high. Actually, if you look at it from a profitability point of view, more than 80% of it is aluminium, 20% is copper.
And since you touched upon prices, and we talked about aluminium going into cars, for example, what's the price differential there? Sure, we want aluminium. It's stronger. Electric vehicles will need it.
Price differential versus steel?
Yeah.
Look, aluminium is one third the cost weight of steel and three times as expensive as steel. But what happened was very interesting, because a friend of mine who makes luggage, I asked him, why are you switching to aluminium when it's more expensive? He says that with steel, if I have to use one kg, with aluminium, I can use half a kg, because I can make thinner aluminium that's as strong and looks better and doesn't corrode. You also have the fact that it may be three times more expensive, but you can use less aluminium to do the same work, which is why it's working out in cars. All planes are aluminium. All fighter planes are aluminium because of that. You can make it extremely thin, but very strong.
And it's interesting you mentioned luggage, because that's an industry one would not have thought would have existed till, let's say, someone like a RIMOWA came and made it cool. I know that you've talked about fashioning your products for your customers and going more downstream in that sense. Is luggage one of those areas as well?
Absolutely. Luggage, furniture, by the way, your coffee capsules, they're all aluminium capsules—-Nespresso. And we have now set up a line so that because they wanted 100% recycled aluminium, and only aluminium can do that. There are numerous sectors that are opening up where the look of aluminium, the anodised finish of aluminium, all that is attractive, besides the sustainability and recycling factor.
It's interesting you mentioned Nespresso, because Nespresso rightfully makes a big deal of collecting the capsules which are used and then bringing them back back. In Hindalco today, how are your logistics divisions split in terms of their work and their focus?
The complexity and the importance of logistics is becoming extremely critical. I mean, during the Covid times, it got very rudely thrust in our face, the importance of logistics. Absolutely, I think that technology is playing at its roots. Today, at any time, there could be about 5,000 trucks of Hindalco on the road. We know exactly where each truck is today. We are all GPS monitored. We have a control tower. We know if the driver has diverted for even half an hour. This whole optimisation of logistics, getting to make sure, as you said, that all the things get picked up and brought to the right place, it's now, how should I put it, a core part of manufacturing.
Not just procurement, but logistics has become core to manufacturing now.
From your point of view, what are the parameters that you track on a daily basis? I mean, between, let's say, output input, input split into raw material, recycling, and the logistics of it, and, of course, the price and everything else.
That's interesting. As you said, I have a dashboard in my office, so I can see all the production numbers. And in aluminium, they tend to be fairly stable. I watch if it's not stable, otherwise, day-to-day production doesn't change much. I think that for us, what is more bothersome is, are we getting enough coal reaching the power plants, the movement of coal, the amount of rakes that we got or did not get. It's funny, but I watch procurement and logistics more closely than I watch output, because if these things are working, the output will come. If the plants get enough material, they're going to produce.
And would you say that's the same for any CEO in a metals company anywhere in the world?
I think aluminium more. Aluminium more, because the input and the logistics have become very critical. I think probably steel is more or less the same, I would say.
And what about copper?
Copper, there it is very interesting, the power and let's say the logistics from an input point of view are not as critical. What you watch is the concentrated movement that happens in ships, which have got a long three month cycle. It's not a daily thing that you watch, but a ship sailing from Chile or Peru has to reach us at certain times of the year, otherwise you will fall short of concentration. That is becoming something—that the shipping movement, the shipping lines, these are becoming critical from a copper point. India does not have copper concentrate.
Has something changed in this versus, let's say, again, a decade ago after Covid?
Everything changed after Covid. See, what has happened was that the majority of the shipping lines were working between the US and China, and that chain got broken during Covid when different ports went into lockdown. Now all those chains are being reestablished. But now the Middle East has become a big hub. And if you see Dubai, Abu Dhabi, they are starting to own more ships and control. I think that what people in India and the government have realised is that having ports and ships that you control is going to be crucial. If you're just relying on international shipping lines and chains, then when trouble happens, suddenly you will find that nobody's landing in your ports anymore.
How do you see the world now? We have a war in Ukraine. We have tension in the Middle East. I'm not seeing this itself causing any direct impact on what you're importing right now. But I'm sure it has a play in the way of the cost of logistics.
Actually, I was reflecting on it a few days back. If these wars had happened, let's say pre-Covid, then any one of them would have caused absolute chaos in the market. Prices of gold would have gone up and every stock market would have crashed. You have now had a fairly serious problem in the Middle East. The markets barely—-maybe one day they did something and it's like… I think what has happened is that companies, countries, post-Covid have become in some ways very competent in what I would call crisis management. Nowadays, if a crisis happens, people are prepared. Immediately they thought, okay, the crisis happened there. I need to divert my shipping lines. I need to watch the movement of goods. And they sort of are able to contain… they don't nervously react. I think the world post-Covid is a lot more tuned to crisis management. As companies now, we don't panic very easily. We are well set.
When you say crisis, you mean logistics mostly.
Well, it could be logistics, it could be demand side. Very often when you have a problem like the Ukraine war. Immediately people thought X would not be in supply, Europe would not get this material from Ukraine. All commodity prices momentarily spiked.
Yeah, wheat. I mean, India banned exports.
A lot of what I would call very short-term decisions were taken. This war round, everybody is calmer, because they have realised that all these things need not happen. Everybody has got plans in place. Everybody knows how they have to adjust. I mean, in some ways, it's very sad that you can have a big crisis and really the world is sort of going on fairly business wise, fairly normally. I mean, it can still escalate and go out of ….
And last question. China plus one. We didn't touch upon it because in a way, I'm assuming it's already subsumed in everything else you've said. But is that a specific area for you in terms of either moving or attracting fresh or are you setting up fresh investment because you feel that, let's say, America is going to import less from China or other countries may import less from China?
We are actually doing, I don't know, numerous projects to cater to the demand driven by that China plus one strategy. I personally believe that for Indian manufacturing, this is probably the most golden opportunity we can ever get. Probably will ever get. And we better take advantage of it because everybody is ready to make that investment in India. Now we need to just get past all our internal issues that we have, because getting land in India is not cheap. Getting environmental clearances in India is not easy.
I mean, we are not China, right? Here we have laws and regulations, and we care about people and communities. What people will find is that India is an opportunity, but it will take some time. It's not as easy. I mean, Chinese people say you can go and have something up and running in a year, but it's not possible here.
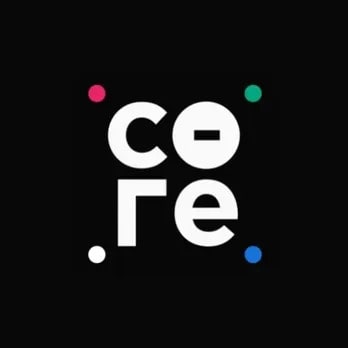
For The Core Report: Weekend Edition, Pai spoke to financial journalist Govindraj Ethiraj on the company's core business and how it is now evolving.